Industrial Hygiene Services: Hazard Exposure Assessments
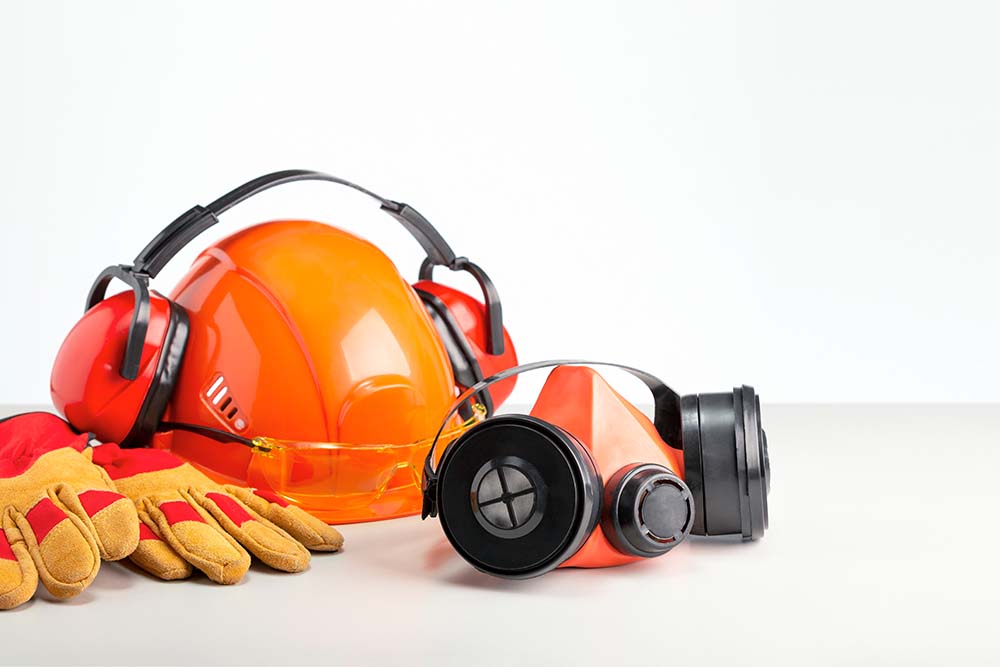
What is Industrial Hygiene?
Industrial hygiene services protect and enhance worker health through identifying, evaluating, and controlling environmental hazards in the workplace that impair health, cause sickness, or contribute to significant discomfort among employees.
Air Monitoring
Air monitoring, a vital service of industrial hygiene, involves the detection and quantification of airborne hazards, including welding fumes, hexavalent chromium, silica, respirable dust (also known as nuisance dust), and volatile organic compounds (VOCs) emanating from paint booths.
Setting Up an Air Monitoring Study
We design an air monitoring study to meet each organization’s unique requirements. It begins by evaluating the chemicals used in the facility and the types of particulate matter employees may be exposed to. We work with clients to understand their manufacturing processes, the activities performed (i.e., welding, painting, cutting, grinding), and the facility’s layout. This holistic understanding aids in determining which employees and areas need monitoring and for what specific contaminants.
We review safety data sheets to identify the chemicals requiring monitoring and to understand where respiratory protection may be necessary. These sheets also detail the permissible exposure limits, guiding the monitoring process to ensure compliance with established safety standards. Once the planning phase is complete, we conduct the on-site monitoring, employing various tools and techniques to capture accurate data regarding employee and environmental exposure to hazards.
From Monitoring to Corrective Action
The data collected is analyzed post-monitoring, and we generate a comprehensive report. This report outlines the findings for each individual and area monitored, offering recommendations based on the levels of exposure observed. Should the results indicate exposure at or above the action level or permissible exposure limit, tailored advice is provided on mitigating the risks to employees, from implementing engineering controls to adjusting work practices and using personal protective equipment (PPE).
Noise Monitoring
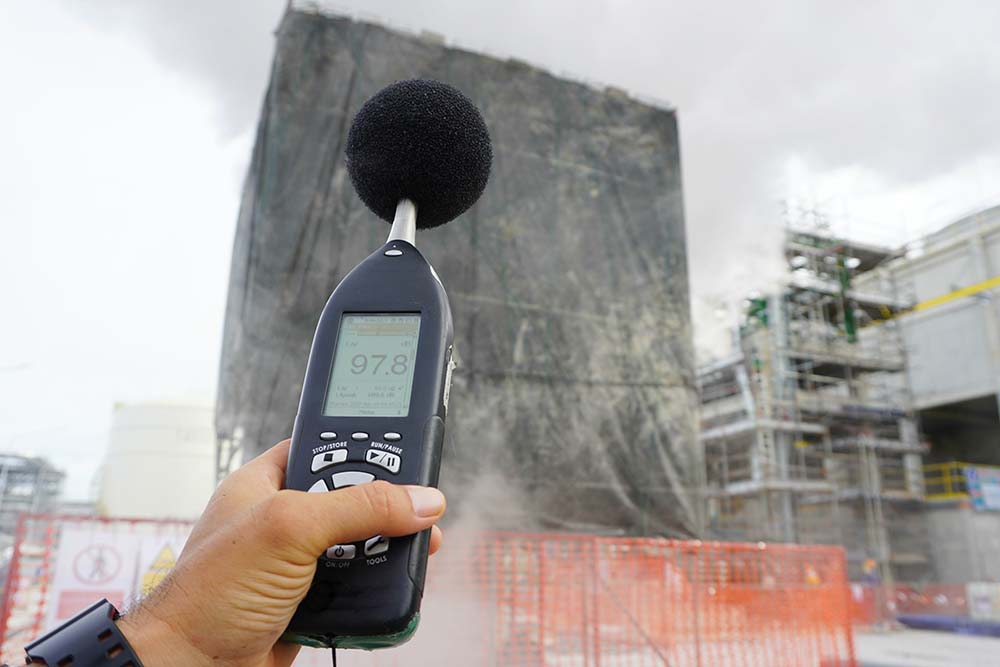
Once assessment and reporting on noise levels are complete, we implement solutions to mitigate noise exposure. These solutions can range from engineering controls, such as installing sound-dampening materials, to administrative controls, like adjusting shift rotations to minimize exposure time and providing personal protective equipment (PPE) like hearing protectors. Additionally, employers and employees receive continuous education and training to recognize and understand the risks of noise exposure, ensuring everyone knows the importance of protective measures and how to use them effectively. This comprehensive approach ensures ongoing employee protection and supports employers in complying with safety regulations, ultimately fostering a safer workplace culture.
Silica Monitoring
Silica, a common mineral in various construction materials like sand and concrete, presents significant health hazards when its fine particles are inhaled. These particles can potentially cause severe diseases such as silicosis and lung cancer. Given these risks, industries such as construction and stone cutting require stringent monitoring of airborne silica to safeguard worker health and comply with occupational safety regulations. The adverse health outcomes associated with prolonged exposure to respirable crystalline silica highlight the necessity of monitoring, making effective control and prevention measures critical.
OSHA mandates precise silica exposure limits, which necessitate rigorous monitoring. Such customized silica monitoring is a fundamental component of industry-specific health and safety protocols. Regular training and education to enhance employees’ awareness of silica risks are also beneficial to promoting safe work practices.
Safety management strategies will incorporate engineering controls and protective measures based on the monitoring outcomes to mitigate silica exposure. These comprehensive measures allow you to meet legal and regulatory requirements and significantly improve your employees’ health and safety conditions.
Welding Fumes Monitoring
Welding processes, utilized in many industries, release a mix of metal fumes and gases that are harmful to health, necessitating monitoring to protect workers and comply with safety regulations. Substances like hexavalent chromium, manganese, lead, and aluminum found in welding fumes pose severe health risks, including respiratory and neurological disorders, making monitoring essential for identifying and managing exposure levels effectively.
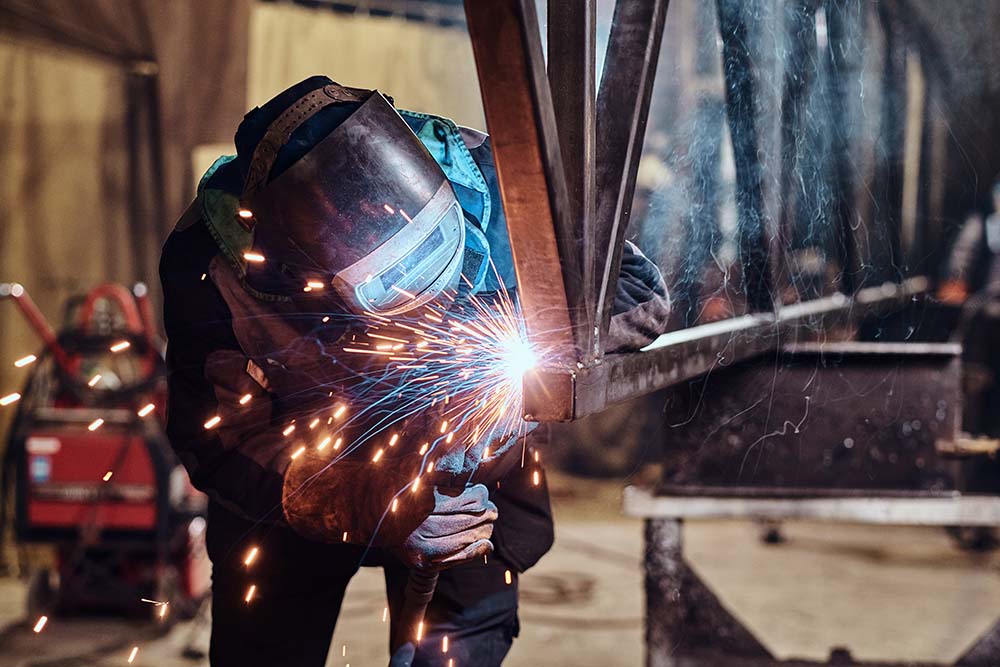
At Safety Consultants USA, we stress the importance of exposure control strategies and employee education to mitigate risks associated with welding fumes. Recommendations include installing local exhaust ventilation, using alternative materials, and ensuring workers wear personal protective equipment. Training programs on health risks and preventive measures educate workers and enhance the effectiveness of safety protocols, reinforcing the organization’s commitment to a safe workplace.
Risks of Paints and Coatings
Managing hazards linked to paints and coatings—such as solvents, urethanes, and epoxies—is essential due to their prevalence in various industries and potential health risks from chemical exposure. These materials, including volatile organic compounds (VOCs) and isocyanates, pose significant dangers through inhalation and direct contact. Monitoring these risks in industrial settings is crucial, as these substances can affect employee health adversely, leading to conditions ranging from respiratory irritation to more severe reactions like asthma.
Our industrial hygiene services ensure that workplaces adhere to established safety standards, protecting workers from immediate and long-term health issues. Monitoring air quality for VOCs and particulates in areas where these substances are used is a primary method to maintain safe exposure levels. Implementing control measures based on air quality data, such as improved ventilation and using safer materials like water-based paints, will reduce potential health risks.
Employee education on the safe handling of paints and coatings, along with the consistent use of personal protective equipment (PPE), is fundamental to ensuring safety in the workplace. Regular training on the health hazards associated with these substances and the correct usage of PPE helps safeguard against exposure. Additionally, it is vital to continuously review and adapt safety measures to respond to changes in the industrial use of these materials, maintaining a safe working environment and ensuring compliance with health and safety regulations.
A Comprehensive Approach to Industrial Hygiene and Safety
Safety Consultants USA takes a meticulous and comprehensive approach to ensure workplace health and safety through its industrial hygiene services. The process involves several key steps, from initial assessment to implementing changes, training workers, and ongoing facility monitoring. Here’s a detailed look at how Safety Consultants USA operates to safeguard workplaces across various industries.
1. Initial Facility Assessment and Dialogue
The process begins with an in-depth evaluation of the facility. Safety Consultants USA engages in detailed discussions with clients to understand their operations, chemicals used, and potential employee exposures. By reviewing facility maps and discussing specific activities like welding, painting, or grinding, consultants can pinpoint areas of concern and identify which employees and spaces require monitoring. This step ensures a tailored approach that addresses each client’s unique needs.
2. Review of Safety Data Sheets and Identification of Hazards
The assessment phase involves reviewing safety data sheets for all chemicals used within the facility to determine which substances require monitoring and to understand where respiratory protection might be needed. Safety data sheets also provide information on permissible exposure limits, guiding the subsequent monitoring process to ensure that exposure levels stay within safe limits.
3. Conducting On-Site Monitoring
Following the initial assessment, Safety Consultants USA schedules a day to conduct on-site monitoring. Our industrial hygiene consultants use specialized equipment to monitor air quality and noise levels, focusing on areas and employees identified during the assessment phase. On-site presence allows consultants to ensure the accuracy of the monitoring process by preventing interference and ensuring that equipment operates correctly throughout the monitoring period.
4. Analysis of Results and Report Generation
Once we complete monitoring, the collected data is analyzed directly or sent to a laboratory for processing. We then compile a comprehensive report detailing individual and area-specific results. This report includes recommendations for mitigating exposure to identified hazards, such as the need for engineering controls, changes in work practices, or the use of personal protective equipment (PPE).
5. Development and Implementation of Corrective Action Plans
Based on the findings of the monitoring report, Safety Consultants USA works with clients to develop and implement corrective action plans. These plans may involve installing new ventilation systems, adjusting work processes to minimize exposure, or introducing specific types of PPE. The goal is to reduce hazardous exposures to acceptable levels, ensuring the safety and health of employees.
6. Worker Training and Education
An essential component of the corrective action plan involves training and educating employees about the identified hazards, the importance of the implemented changes, and how to use PPE correctly. Safety Consultants USA provides comprehensive training sessions covering everything from exposure-related health implications, proper fit of required PPE, and maintenance of PPE. This education ensures that workers are protected and knowledgeable about their safety.
7. Ongoing Monitoring and Reassessment
Safety Consultants USA recommends ongoing facility monitoring to ensure the continued effectiveness of implemented changes. This work may include regular air and noise monitoring to assess the impact of new equipment or changes in production processes. Ongoing reassessment allows for timely adjustments to the safety plan, ensuring it protects employees effectively.
Industrial Hygiene Services Across Various Industries
Safety Consultants USA offers a suite of industrial hygiene services tailored to the unique needs of various industries. Each sector faces specific challenges and risks, requiring specialized approaches to ensure the health and safety of workers. Below is a detailed breakdown of the different industries that utilize these services, the types of services applied, and the reasons behind their necessity.
Metalworking and Fabrication
Industries
Includes welding, metal composite manufacturing, and structural steel fabrication.
Services Utilized
Air monitoring for welding fumes, hexavalent chromium, and respirable dust. Noise monitoring is also significant due to the high decibel levels produced by metalworking machinery.
Why They Need It
These services are essential for assessing and controlling workers’ exposure to hazardous fumes and noise, which can lead to respiratory issues and hearing loss.
Construction and Stone Working
Industries
Stone cutting, concrete, and block manufacturing.
Services Utilized
Silica monitoring is critical in these industries, given the high silica content in materials like concrete and stone, which can lead to silicosis upon inhalation.
Why They Need It
Silica monitoring helps ensure compliance with OSHA standards for silica exposure, protecting workers from long-term respiratory diseases.
Manufacturing and Engineering
Industries
This broad category includes HVAC component manufacturing, custom millwork and cabinetry, and the production of interior train car materials.
Services Utilized
Air monitoring for VOCs and particulate matter and noise monitoring to protect against chemical exposures and auditory hazards.
Why They Need It
These services help identify hazardous exposures in complex manufacturing processes, ensuring a safe working environment.
Automotive Industry
Industries
Car restoration, including companies specializing in rebuilding classic Ford Broncos and Land Rovers.
Services Utilized
Noise and dust monitoring, particularly for grinding and painting tasks.
Why They Need It
It safeguards against respiratory hazards from dust and paint fumes and hearing damage from high noise levels during restoration processes.
Food Processing Equipment Manufacturing
Industries
Manufacturers of equipment for poultry processing.
Services Utilized
Noise monitoring due to the loud nature of the machinery used in fabricating equipment for food processing.
Why They Need It
Ensuring employee hearing protection and compliance with permissible noise exposure levels regulations.
Decorative and Home Decor Manufacturing
Industries
Production of items such as pillows, beanbag chairs, and outdoor planters.
Services Utilized
Noise monitoring, given the unexpected noise levels produced by machinery in the manufacturing process.
Why They Need It
To protect employees from noise-induced hearing loss in industries not typically recognized for high noise levels.
Paint Booths Across Various Industries
Industries
Auto manufacturing, restaurant interior manufacturing, custom millwork, and cabinetry.
Services Utilized
Air monitoring for VOCs released during painting processes.
Why They Need It
VOC monitoring is essential for minimizing employees’ exposure to harmful chemicals, which can lead to long-term health issues.
Specialized Services
Industries
National cemetery headstone inscription services.
Services Utilized
Silica and noise monitoring due to the cutting and engraving processes involved in stone inscriptions.
Why They Need It
To comply with VA requirements for annual noise and air monitoring and ensure worker safety during the inscription process.